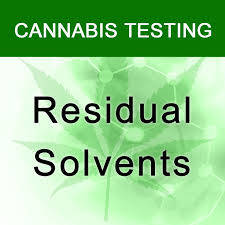
By Seth Wong and JJ Slatkin
On February 1, 2018, the State of Colorado, Marijuana Enforcement Division implemented new residual solvent testing requirements for concentrate manufacturers. The new rules included lower permissible values (thresholds) for existing analytes like Butane and added new compounds which had not previously been screened for such as Isopropyl Alcohol. (Colorado’s rules can be found here: https://www.colorado.gov/pacific/enforcement/med-rules) The new rules threw the industry for a loop. Many of the new compounds required under the new rules existed in most cannabis manufacturing facilities, whether or not they were used in the processing of cannabis products.
Once the new testing rules went into effect, one of the biggest culprits that came up positive on the Residual Solvent Analysis was Isopropyl Alcohol (IPA). While TEQ Analytical Labs did find many positives for these two compounds, they were rarely over the state threshold and did not result in a failed analysis. Manufacturers were concerned about this newly discovered contaminant and insisted that they were not using IPA while processing products. However, the manufacturers did not consider that they were potentially using these products to clean their facilities or their equipment and or other potential sources of their contamination.
Isopropyl Alcohol is commonly found throughout our every-day lives. Isopropyl Alcohol (IPA), for instance, is a primary cleaning agent that many Marijuana Infused Processors (MIPs) employ to clean their extraction equipment and facility. At TEQ, we saw a direct correlation between a customer’s cleaning agents and practices and positive hits for IPA in their production runs. Production runs analyzed after equipment was cleaned with IPA had a large amount of contamination, some of which caused failures for clients. Then as the client processed more and subsequent batches through the equipment, we could see the presence of IPA in products decline and eventually trail off.
Some residual solvent contamination detects may not be caused by environmental contamination but may be trace residual contamination in the ingredients utilized during the manufacturing process. For example, Butane. Industrial Grade Butane is not as pure as Ultra High Purity Butane. Therefore, a manufacturer creating extracts with industrial grade Butane could potentially introduce more contaminants into their product than if they had used UHP Butane. It is also important to understand how your gas tank works. A full tank of gas may appear to have less contaminants when processing. However, as a processor uses more gas from the tank, those contaminants may concentrate into the remaining gas in the tank. If you used the entire tank, the last bit of gas may have more contaminants than desired and lead to residual contamination in your product.
From my previous experience in the laboratory testing world, I, as well as many testing lab employees, have encountered manufacturing and laboratory practices and procedures that are designed to prevent residual contamination like this from occurring. Often you will see food facilities, environmental facilities, and testing labs that have adopted rules, Good Manufacturing Practices (GMPs) and Good Laboratory Practices (GLPs) indicating what products and supplies are permitted in a facility. This is done to;
- Prevent accidental introduction of an incorrect product into the work flow
- Prevent intentional introduction of an incorrect product into the work flow
- Ensure no potential environmental contamination
Additionally, there are often policies that apply to employees related to their personal hygiene and habits. Many food and testing companies have employee policies that prohibit employees from wearing cologne or perfume because of residual alcohols that are present in those fragrances that could impact the product and/or quality control analysis.
TEQ helped clients troubleshoot their suspect findings and clients began scrutinizing the inputs they were using when manufacturing. Because of the new threshold levels and screening for new compounds, the industry was finding new suspect hits for solvent contaminants they had not considered under the previous rules nor had on their radar. Together we asked; How were clients cleaning equipment? What were they using to clean equipment? How much time elapsed between cleaning and the next batch of processing? These new contaminant hits helped reinforce the best practices used in the food industry. Having detailed, articulate cleaning plans that allow enough time for the equipment to be cleaned before the next batch of processing and more importantly, utilizing food grade cleaners since many cannabis products are ingested, would help prevent unnecessary contaminant detects.
To prevent residual contamination, TEQ recommends that clients know and understand all inputs utilized during their manufacturing practices. Read your labels and understand your products. The best place to start is by asking your vendor. In the case of butane or other extraction gasses, inquire with the gas vendor the grade of gas that is being purchased and utilized and what other contaminants the gas company suspects or is testing for in their gas; we even recommend requesting a COA. Know what products are in your facility and specify where, when, and how they can be used. In some cases, you may have to entirely remove certain products from your facility and need to source a different product that will clean your equipment without leaving behind any residual hazardous contamination.
TEQ also recommends setting parameters for the products in your facility. What purity gas are you willing to use? Will you allow your employees to use the entire tank or stop when the tank is down to its last 1/8th? Consult your vendors to understand more about the products you are buying and understand their limitations and how those limitations can impact your operation.
Finally, if you have reviewed all product inputs, checked labels, and certified supplies and are still having failures, verify that all equipment is functioning properly. Recently, a client’s vacuum ovens appeared to be working correctly but the heating element wasn’t engaging as expected, leading to far less purging of residual solvents. Alternatively, we have seen distillation systems that couldn’t sustain a constant pressure, leading to incorrect fractionalization that was incomprehensible analytically until the vacuum issue was identified. Utilize a HACCP (Hazard Access Critical Control Point) Plan to identify these high-risk areas, how to police them, and most importantly how prevent them from becoming issues. In short, numerous issues may be present, some of which may be unknown to you and could be impacting your samples.
Understanding ingredients and all the products, such as regular every day cleaners, in your facility are key to preventing unknowns from entering your production process. Implementing employee best practices, manufacturing specifications with regular system checks, like the case of the vacuum oven, and HACCP plans are key to rounding out good manufacturing practices. Finally, a good working relationship with your laboratory can help you troubleshoot any suspect results. It’s vital to know the specifics of the products and systems used during the manufacturing process, regardless of the role they play, as they could be the root cause of suspect analytical results.